|
Pièce A |
Pièce B |
Pièce C |
Pièce D |
Pièce E |
 |
 |
1.16 |
1.20 |
1.22 |
1.09 |
1.11 |
10% |
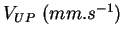 |
25.68 |
25.17 |
24.91 |
26.01 |
25.86 |
4.2% |
 |
1.16 |
1.20 |
indéfinie |
1.09 |
0.82 |
32% |
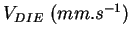 |
13.19 |
13.58 |
indéfinie |
13.66 |
14.66 |
10% |
 |
0.43 |
0.52 |
0.22 |
0.25 |
0.39 |
58% |
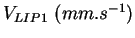 |
13.19 |
15.35 |
18.94 |
13.47 |
12.25 |
35% |
 |
1.03 |
1.05 |
0.97 |
0.85 |
0.96 |
19% |
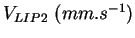 |
20.18 |
20.46 |
21.03 |
23.02 |
19.44 |
16% |
|
|
|
|
|
|
|
|